It is well known that equipment, technology, and craftsmanship in PCBA all affect the boards quality, and the other part is what we will discuss here, that is, components. Components are the core components of the circuit board, and the quality of components is directly related to the final quality of PCBA. The component market is mixed, and how to avoid fake components is an essential skill for a professional PCBA manufacturer.
The current components market is a quite chaotic, which means not only the price is unstable, but the quality is also uneven. Some people take advantage of the chaotic opportunity to sell dismantling materials, scraps, and three-no bad quality products. This has greatly tested the ability of various PCBA factories to identify fake components.

Commonly Used Methods To Identify Fake Components
1. Visual Inspection
The easiest way to check for fake components is visual inspection. This includes checking the part numbers and silk screen markings on the components against the specifications provided by the source manufacturer. In addition, you can use previous data and products purchased from suppliers in the past to verify the validity of the date code. Other aspects of the visual inspection are as follows:
Fraudsters may use black layers to place different part numbers and date codes on components. It involves applying a thin black epoxy coating on the top of the component and then roughening the surface to obtain the desired texture. It also includes matching the font to the original font. In order to determine if there is a power failure, it is important to check the top and surface texture of the components. In addition, it is necessary to compare the manufacturer’s symbol with known original components.
Before proofing Assembled PCB, you should also check whether the leads of the components are damaged, re-tinning, etc. This is part of the incoming inspection and cannot be ignored due to the tight delivery time.
Other factors that need to be considered in the device include component orientation, overall appearance, contact conditions, and visual inconsistencies.
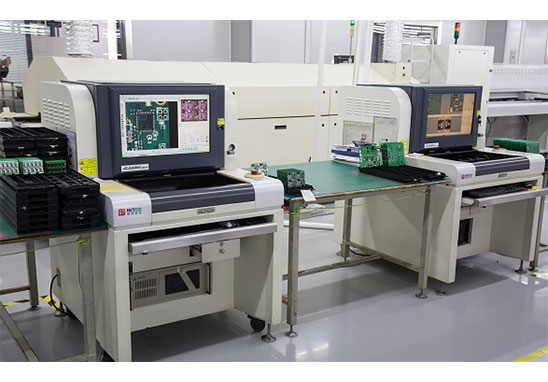
2. Electrical Test
Electrical testing of fake electronic components involves verification of resistance and capacitance values and full-function analysis of active components. Various contract manufacturers (CM) and third-party test laboratories have electronic test facilities. In order to test complex products, expensive test setup and programming expertise are essential, which can only be achieved in OCM or some third-party laboratories. When the main component is abnormal, you can also apply to the source factory for evaluation.
3. X-ray Inspection
X-ray inspection of hidden/internal characteristics of components. When comparing, it is always beneficial to have a gold standard or a famous example. This method checks and verifies the physical dimensions, lead frame and connection wires. In addition, it also checks for any internal changes in all components.
4. XRF Technology
XRF stands for X-ray fluorescence spectroscopy. This technology determines the elemental composition of materials and is most suitable for verifying RoHS compliance.
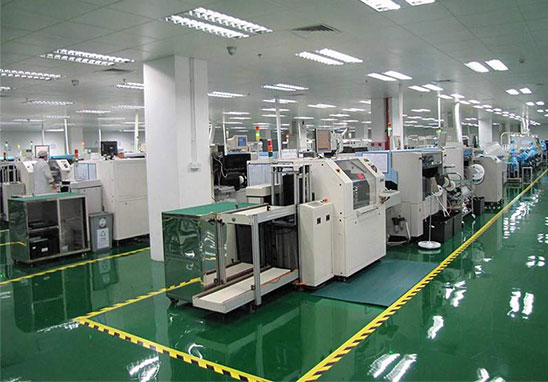